Understanding Reactive, Preventive and Predictive Maintenance
Summary
The blog discusses the importance of maintenance in fleet management and the different types of maintenance – reactive, preventive, and predictive. It highlights the common expenses faced by truck owners, the impact of electronic components on maintenance costs, and the pros and cons of each maintenance type. The article emphasizes the need for regular monitoring and analysis of equipment to avoid severe malfunctions resulting in higher expenses.
Fleet management is the most significant aspect of any successful logistics. As much as the performance of the fleets is important in the logistics, maintenance is equally important for a cost effective business. The balance between the performance and its maintenance is a key in fleet management to run a cost effective business.
Performance and efficiency of your fleets is always directly proportional to the maintenance level. Higher the maintenance of your fleets, higher will be the performance.
Lower the monitoring and maintenance, lower will be the performance and also higher will be the expense as the condition of the vehicle gets worse due to lack of maintenance for a longer period.
With increased technology and electronic devices incorporated into the fleets, the importance of maintenance has eventually increased compared to earlier days.
Any fleet that is not well maintained or not monitored regularly will result in unexpected anomalies during the fleet operations, which would cost much higher for the companies to handle. Further let us discuss in detail about the various maintenance costs faced by the truck owners.
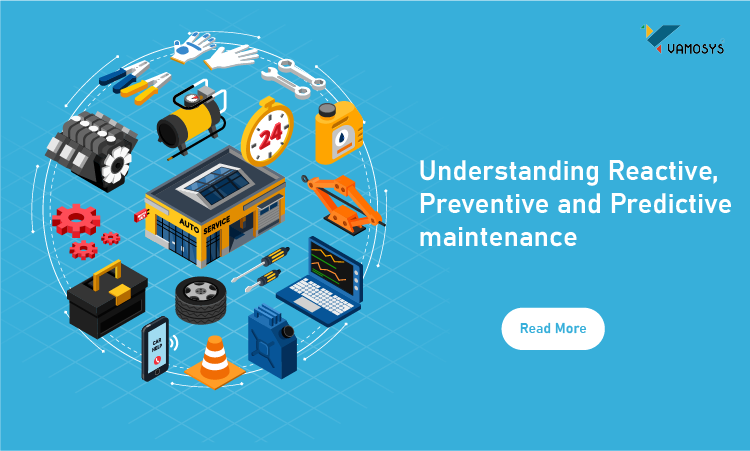
How much maintenance cost occurs for truck owners?
Maintenance costs of trucks differ with every individual owner based on the quality of their management and type of vehicle used. In general there are common expenses faced by the truck owners like, water wash, change of engine oil, air checks, brake repairs, change of tyres annually based on their conditions, replacement of fresh wirings, lights, clutch plates and other electronic equipment that involves sensors and other micro processors & controllers.
For an effective maintenance of your fleets, excluding the fuel costs, on average, it costs approximately 10% of the total expenditure of a company per year just for the maintenance purpose. In case of severe damage, repair works after collisions or breakdown and other maintenance works related to electronic components would cost higher.
In modern day trucks, more than the general services, the maintenance of the electronic components is very much important as their maintenance costs are much higher compared to other physical components of the trucks.
And also these electronic components provided by various telematics services handle the most important functions of the fleet in logistics. Hence it needs regular and systematic monitoring and analysis of their functions.
And the datas related to their functioning has to be recorded consistently by the management for the better analysis of the equipment to avoid severe malfunctions resulting in higher expenses.
Considering the modern day trucks with lots of Internet of Things (IoT) and electronic devices, there are various methods of management with respect to its maintenance types like reactive maintenance, preventive maintenance and predictive maintenance. Let’s discuss in detail about these types of maintenance with their merits and demerits.
Reactive Maintenance
Reactive maintenance is the process of reacting or initiating the maintenance process after the damage of the product. Once the truck faces breakdown due to any engine related issues, then the management takes appropriate actions to resolve it.
These types of maintenance are definitely harmful for any company as it increases the cost of maintenance or the replacements of the damaged components. In reactive maintenance, most of the case involves replacement of components rather than repairing it.
Accidents and collisions cause reactive maintenance processes that are unpredictable. There are several disadvantages compared to its advantages. Advantage would be low maintenance cost initially and no regular monitoring involved in this type of maintenance.
There are several disadvantages like, higher maintenance cost, lower life span of the component, higher fuel consumption, reduced reputation due to unexpected delays.
Life span of any product that is not maintained regularly is very low. The working efficiency decreases as the days pass. Greasing the movable objects and applying filters wherever needed reduces the risk of malfunctions and reduces the fuel consumption by 10-15% with smooth movements.
And in these types of reactive maintenance practices, a company faces unplanned activities like breakdown during the important operations that are time bound. This type of maintenance results in delay in delivery of the goods that spoil the company’s reputation.
Preventive Maintenance
Preventive maintenance is the process of inspecting the vehicle or a component just before it gets damaged completely. Hence it’s called preventive. Preventing it from the severe damage makes it fall between the reactive maintenance and the predictive maintenance.
How does the company or the management get to know that the truck or a product is about to face any anomaly?
It is the process of maintenance that functions based on two main strategies like time based maintenance and usage based maintenance.
Time based maintenance is the process of inspecting the vehicle or the component after a particular point of time, for example a component has a warranty of 1 year duration. The management uses the product for one year without any monitoring and inspects it after a year inorder to avoid any malfunction.
Another strategy is maintenance based on its usage. There might be a vehicle with high load capacity. Obviously the vehicle will be used more compared to other vehicles with lower load capacity. Hence, higher the usage of the vehicle, higher will be the maintenance cost.
Maintenance based on usage is a kind of preventive maintenance where the management looks at the vehicle’s long performances and inspects its components to prevent severe damages.
Predictive Maintenance
Predictive maintenance is the process of monitoring the vehicle and its components while its performances are absolutely normal. Prediction maintenance has its own standard set for the functions of each component.
Consistent monitoring of the vehicle and its performances enable the management team to know if there is any deviation in the performances from their standard of operation. If there is any, management takes immediate actions to maintain the performance standards of the vehicle and its components.
Predictive maintenance is very much different from preventive maintenance. Predictive maintenance does not allow chances for any malfunctions as it involves regular condition monitoring.
Quantitative maintenance is also another significant aspect of predictive maintenance that involves the measurement of various parameters like heat, vibrations of the components. Any deviations in the limits of operating standards, the problems are reported immediately to avoid the anomalies.
There are several advantages, it reduces the risk of severe damage caused to your fleets through continuous monitoring. This technique is widely adapted due to its higher efficiency and being cost effective.
Predictive maintenance helps in increasing the reputation of the company by delivering the products at the right time without any malfunction or breakdowns. Maintenance costs are also very low as the vehicle and its components are monitored regularly and repaired with very lower frequencies of malfunctions.
There are several equipment like radiometers, vibration pens, Ultrasonic meters that are used during the operations to inspect the motors and other electronic devices for any malfunctions
Apart from these equipment, there are several facilities provided by the telematics services through the GPS tracking devices that also help in the maintenance of the vehicles.
Predictive maintenance keeps the fleet management team active and responsible for every operation that counts for the successful trade in the logistics industry.
Sushanthi
Sushanthi is a Content Writer who wishes to be the voice of brands to project their innovative ideas and stories through her writing skills.